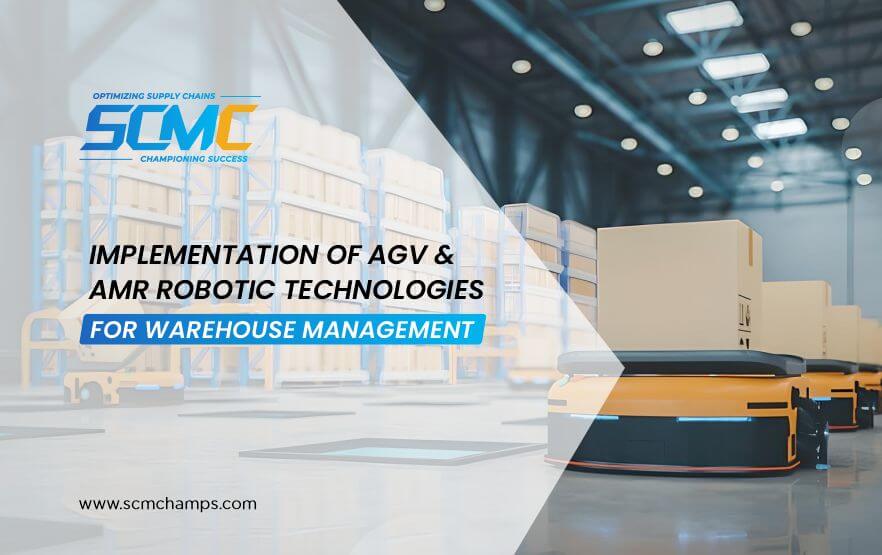
In today’s fast-evolving supply chain landscape, warehouses play a crucial role in ensuring efficient product storage, retrieval, and distribution. The rise of e-commerce, increased consumer expectations, and the need for rapid fulfillment have forced warehouses to seek innovative ways to stay competitive. Among the technological advancements, Automated Guided Vehicles (AGVs) and Autonomous Mobile Robots (AMRs) have emerged as transformative solutions for warehouse management. Integrating these robotic technologies into SAP warehouse systems can revolutionize operations, bringing efficiency, accuracy, and scalability.
In this article, we explore the implementation of AGV/AMR robotic technologies for warehouse management, the benefits they bring, and how SAP’s warehouse solutions—such as SAP Extended Warehouse Management (EWM)—enable this automation.
The Evolution of Warehouse Robotics
Traditionally, warehouse management has relied heavily on human labor for material handling, storage, and transportation tasks. While manual processes have their merits, they are prone to errors, inefficiencies, and scalability limitations. The introduction of robotic systems such as AGVs and AMRs is helping warehouses transition from labor-intensive operations to fully automated environments.
AGVs are robots that follow predefined paths within the warehouse. They are particularly useful for repetitive tasks such as transporting goods from one location to another. AMRs, on the other hand, use advanced sensors and AI to navigate dynamically without requiring predefined paths. This makes AMRs more adaptable in complex and changing warehouse environments. Both AGVs and AMRs contribute to warehouse automation, optimizing material flows and minimizing downtime.
Key Benefits of AGV/AMR Implementation
1. Increased Efficiency
One of the main advantages of implementing AGVs and AMRs in warehouse management is the dramatic improvement in operational efficiency. These robots can work 24/7 without fatigue, increasing productivity compared to human labor. AGVs and AMRs can seamlessly handle tasks such as picking, transporting, and storing goods. With SAP warehouse automation solutions, real-time data can be leveraged to monitor and control the flow of goods within the warehouse. This reduces bottlenecks and ensures faster order fulfillment.
2. Improved Accuracy and Reduced Errors
Human errors in warehouses—such as incorrect picking or misplaced inventory—can have a significant impact on productivity and customer satisfaction. AGVs and AMRs eliminate many of these errors by accurately following the processes defined in the SAP Warehouse Management System (WMS). This improves order accuracy and enhances inventory management. The robots also ensure that goods are stored in their designated locations, reducing the chances of misplaced or missing inventory.
3. Cost Savings and ROI
While the initial investment in AGV/AMR systems may be high, the long-term savings in labor costs, productivity gains, and error reduction can lead to a favorable return on investment (ROI). Robots reduce the need for manual labor, allowing companies to allocate human resources to higher-value tasks such as strategic planning or customer service. The integration of these robotic technologies with SAP Warehouse Automation helps optimize workflows, minimize downtime, and maximize throughput.
4. Scalability
In industries with seasonal demand fluctuations, scaling manual labor to meet peak requirements can be challenging. However, AGVs and AMRs offer the flexibility to scale operations up or down as needed. These robots can easily be added or reprogrammed to accommodate changing warehouse layouts or increased workloads. SAP Warehouse Robotics solutions allow for seamless integration and expansion of automation systems, ensuring that warehouses can scale as the business grows.
SAP’s Role in Warehouse Automation
SAP plays a pivotal role in enabling the integration of AGVs and AMRs into warehouse operations. The SAP Warehouse Management System (WMS), particularly SAP Extended Warehouse Management (EWM), offers robust features to support the implementation of robotics technologies.
1. SAP Warehouse Robotics Integration
SAP Warehouse Robotics provides the framework for integrating AGVs and AMRs with existing warehouse processes. This allows the robots to interact with the warehouse’s WMS to manage tasks such as picking, inventory movement, and replenishment. By automating these tasks, the robots free up human workers to focus on more strategic activities.
SAP EWM’s real-time inventory management capabilities ensure that AGVs and AMRs have the latest data on stock levels, location accuracy, and order priorities. This minimizes the risk of delays or missteps in the fulfillment process.
2. Intelligent Task Scheduling
AGVs and AMRs can operate most effectively when their tasks are intelligently scheduled. SAP Warehouse Automation uses AI and machine learning to allocate tasks to robots based on priorities, current inventory levels, and the overall warehouse workflow. This ensures that robots work in the most efficient manner possible, reducing idle time and optimizing resource allocation.
3. Improved Data Insights
With the implementation of AGVs and AMRs, warehouse managers gain access to valuable real-time data insights that can help optimize operations further. SAP’s WMS offers comprehensive reporting and analytics tools that provide detailed information on robot performance, inventory accuracy, and overall system efficiency. These insights can help in continuous process improvement, allowing for a more agile and responsive supply chain.
Considerations for Implementing AGV/AMR Technologies
While AGVs and AMRs offer a multitude of benefits, successful implementation requires careful planning and consideration. Below are key factors to consider when introducing robotic technologies into your warehouse:
1. Warehouse Layout
The design and layout of the warehouse play a crucial role in determining the success of AGV/AMR implementation. AGVs, which follow predefined paths, may require changes to the physical structure of the warehouse to ensure smooth navigation. AMRs, with their advanced sensors, are better suited for complex layouts, but still require an environment free of obstacles to operate efficiently.
2. Integration with Existing Systems
For maximum efficiency, AGVs and AMRs should be integrated with the warehouse’s existing SAP WMS system. This allows for seamless communication between the robots and the warehouse’s software, ensuring that tasks are executed as efficiently as possible.
3. Training and Maintenance
Though robots reduce the need for manual labor, training is still necessary to manage the automated systems. Warehouse staff should be trained to oversee robot operations and troubleshoot any issues. Regular maintenance is also critical to ensure the longevity and reliability of the robotic systems.
Conclusion
The implementation of AGV/AMR robotic technologies in warehouse management is transforming the way businesses operate. By increasing efficiency, improving accuracy, and providing scalable solutions, these robotic systems offer significant advantages over traditional manual processes. When integrated with SAP warehouse solutions, businesses can further optimize their operations, ensuring they remain competitive in an increasingly automated world.
For warehouses seeking to future-proof their operations, investing in AGVs, AMRs, and SAP Warehouse Robotics will pave the way for sustainable growth and operational excellence. As SAP continues to evolve its automation capabilities, the future of warehouse management will be defined by intelligent, efficient, and highly automated systems.