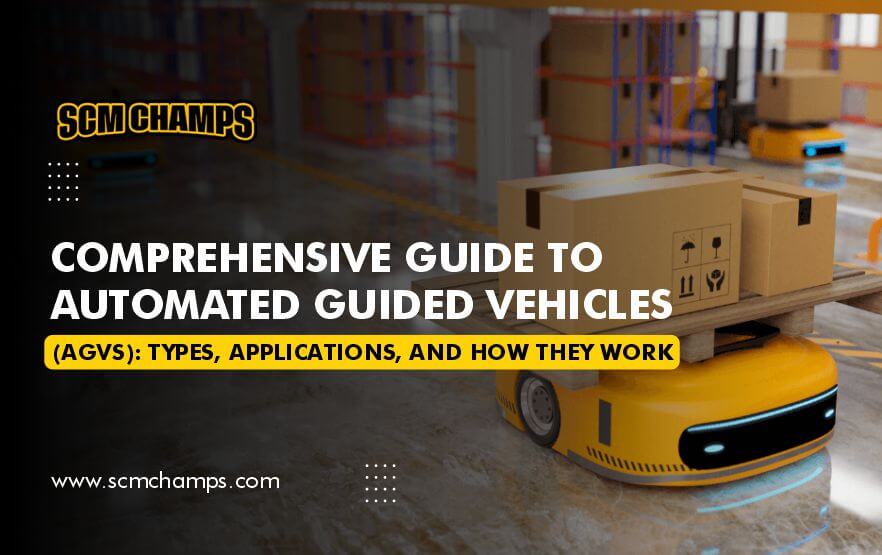
What is AGV in warehouse robotics and how does it work?
Introduction: Automated guided vehicles (AGVs), also referred to as self-guided or autonomous guided vehicles, are revolutionizing material handling operations in warehouses, distribution centers, and manufacturing facilities. These innovative vehicles operate autonomously, offering a wide range of benefits. In this post, we will explore the various types of AGVs, examine their applications, delve into their functionality, and highlight the advantages they provide. Additionally, we will discuss how SAP Warehouse Robotics services integrate with AGVs to optimize warehouse operations and enhance efficiency.
Section 1: Applications for AGVs AGVs are revolutionizing traditional material handling tasks that would typically rely on forklifts, conveyor systems, or manual carts. They excel in repetitive movements of large volumes of materials, offering increased efficiency and productivity. Let’s explore some key applications where AGVs are making a significant impact.
1.1 Material Transportation: AGVs play a vital role in transporting raw materials such as metal, plastic, rubber, or paper. They efficiently move materials from receiving areas to warehouses or even deliver them directly to production lines. With AGVs in action, production lines remain uninterrupted, ensuring a seamless supply of materials without human intervention.
1.2 Work-in-Process Handling: AGVs are instrumental in work-in-process applications, supporting production or manufacturing lines. They facilitate the movement of materials or parts from warehouses to production lines or between workstations. By avoiding delays caused by manual material retrieval, AGVs maintain a steady flow of operations, preventing any interruptions in the manufacturing process.
1.3 Inbound and Outbound Handling: AGVs play a crucial role in inbound and outbound logistics. They assist in replenishment by transporting inventory from receiving areas to storage locations or from long-term storage to forward-picking locations. This ensures that stock is readily accessible for efficient order picking. Collaborative mobile robots, functioning as AGVs, guide warehouse associates through tasks and transport picked orders to packaging and shipping workstations.
Section 2: Types of Automated Guided Vehicles
2.1 Automated Guided Carts (AGCs): AGCs are the simplest type of AGVs, capable of transporting various materials. They employ navigation systems ranging from magnetic tape to advanced AI-based sensor navigation. AGCs find applications in sorting, storage, and cross-docking scenarios. An interesting example is automated hospital cart transporters that efficiently move loads within hospitals, reducing labor costs.
2.2 Forklift AGVs: Forklift AGVs perform similar functions to human-operated forklifts, such as pallet transportation, but without the need for human operators. These AGVs offer increased efficiency and safety in material handling operations.
2.3 Towing AGVs: Towing AGVs, also known as tugger AGVs, pull non-powered load-carrying vehicles in a train-like formation. These AGVs are ideal for transporting heavy loads over longer distances, with multiple drop-off and pick-up stops along a predefined path through warehouses or factories.
2.4 Unit Load Handlers: This type of AGV carries discrete loads or single units, such as pallets or totes containing multiple items. Unit load handlers provide efficient and precise transportation for various objects.
2.5 Heavy Burden Carriers: Heavy burden carriers are robust AGVs designed specifically for transporting extremely heavy loads. Applications include large assembly, casting, and coil and plate transport. Some heavy-burden carriers come equipped with self-loading capabilities and advanced steering systems for enhanced efficiency.
2.6 Autonomous Mobile Robots (AMRs): AMRs represent the most technologically advanced category of AGVs. Equipped with intelligent navigation capabilities like sensors and camera systems, AMRs can detect and navigate around obstacles in real time. These dynamic AGVs can optimize paths within warehouses or facilities, ensuring the most efficient movement of goods.
Understanding the Inner Workings of AGVs: Navigation, Steering, and Traffic Control
AGVs function as self-propelled vehicles guided by sophisticated software and sensors. While most AGVs follow predefined pathways, AMRs employ advanced technology for dynamic navigation. Let’s dive into the mechanics of AGVs’ operational workflow.
Section 1: AGV Navigation AGV navigation relies on various mechanisms, each suited to different environments and requirements. Here are some of the commonly used navigation methods:
1.1 Magnetic Guide Tape: Some AGVs utilize magnetic sensors to follow a predefined track marked with magnetic tape. This mechanism ensures accurate and reliable navigation.
1.2 Wired Navigation: AGVs equipped with wired navigation detect wire paths embedded in the facility floor. The wire transmits a signal that AGVs pick up using antennas or sensors, guiding their movement.
1.3 Laser Target Navigation: Reflective tape mounted on objects such as walls, machines, or poles serves as a guide for AGVs. Equipped with laser transmitters and receivers, AGVs use lasers to calculate the object’s angle and distance, allowing them to navigate efficiently.
1.4 Inertial (Gyroscopic) Navigation: AGVs controlled by computer systems use transponders embedded in the facility floor to verify their course accuracy, ensuring they stay on the designated path.
1.5 Vision Guidance: Vision-guided AGVs rely on cameras to record features along the route. These recorded features serve as reference points for AGVs to navigate autonomously without modifications to the infrastructure.
1.6 Geoguidance: Geoguided AGVs recognize objects in their environment to establish their real-time location and navigate throughout the facility. No infrastructure modifications are required for this navigation method.
1.7 LiDAR: LiDAR (Light Detection and Ranging) is a cutting-edge navigation technology that uses sensors to measure distances between the AGV and surrounding objects. The data collected creates a 360-degree map, enabling AGVs to navigate and avoid obstacles without additional infrastructure requirements.
Section 2: AGV Steering AGVs employ different steering control options to maneuver through various situations. Here are the common types of AGV steering:
2.1 Differential Speed Control: This widely used steering method relies on two independent drive wheels. By adjusting the speed of each wheel, AGVs can turn, move forward, or backward. Ideal for tight spaces, this steering control doesn’t require additional mechanisms but isn’t suitable for towing applications.
2.2 Steered Wheel Control: Similar to steering in cars or trucks, steered wheel control utilizes a turning wheel as the drive wheel. This method offers precise and smooth turning, is commonly used in towing applications, and is sometimes operator-controlled.
2.3 Combination Steering: AGVs equipped with combination steering have independent steer/drive motors on diagonal corners and swiveling castors on the other corners. This configuration allows AGVs to turn in any direction like a car while also offering differential steering mode, enhancing maneuverability.
Section 3: AGV Traffic Control To ensure safe and efficient operations, AGVs employ traffic control measures. Let’s explore two common methods:
3.1 Zone Control: This method involves defining specific areas within the facility where AGVs operate. Transmitters and sensors communicate signals to determine if an area is clear or occupied by another AGV. AGVs receive “clear” or “stop” signals, enabling them to enter or wait until the area is clear.
3.2 Collision Avoidance: AGVs equipped with collision avoidance sensors transmit signals and monitor replies to detect objects in their path. Sonic or optical sensors, as well as bumper sensors, help AGVs avoid collisions by stopping or changing course.
3.3 Combination Control: AGVs incorporating both collision control and zone control sensors offer comprehensive collision prevention. By combining these systems, AGVs can adapt to various situations and ensure safe operations.
The Advantages of Automated Guided Vehicles (AGVs) in Warehousing and Manufacturing
Automated Guided Vehicles (AGVs) have revolutionized the warehousing and manufacturing industries, offering a wide range of benefits. In this article, we explore the advantages of AGVs, including increased efficiency and productivity, consistent costs, flexibility, space optimization, and improved safety. Let’s delve into the transformative power of AGVs and their impact on operations.
Section 1: Increased Efficiency and Productivity AGVs operate autonomously, leading to enhanced efficiency and productivity. They provide predictability and reliability, particularly for repetitive tasks. By eliminating unnecessary walking and physical labor involved in material transportation, AGVs streamline operations and set the pace for workers. Collaborative mobile robots guide associates through tasks, reducing human error and improving order-picking accuracy. Additionally, AGVs leverage AI to optimize routes and prioritize work, ensuring efficient resource utilization.
Section 2: Consistent Costs Compared to human labor, which can fluctuate based on market conditions and demand, AGVs offer consistent costs. Typically acquired on a per unit or per rental period cost basis, AGVs provide stability in budgeting and financial planning.
Section 3: Flexibility AGVs provide flexibility, offering the ability to easily change routes without the need for re-routing guide wires or other infrastructure adjustments. This adaptability allows for efficient adjustments to meet changing operational requirements. AGVs are also scalable, enabling businesses to add additional units based on demand, ensuring a flexible and responsive solution.
Section 4: Space Optimization AGVs require less space compared to other automation solutions like conveyor systems. Their compact size allows for floor layouts with narrower aisles, enabling better space utilization within warehouses and manufacturing facilities. With AGVs taking up less space, businesses can maximize their operational areas.
Section 5: Improved Safety AGVs prioritize safety in warehouses, distribution centers, and manufacturing facilities. Equipped with sensors, AGVs can avoid collisions and navigate around obstacles. Advanced AGVs, such as Autonomous Mobile Robots (AMRs), utilize intelligent routing capabilities to plan the most efficient paths, reducing aisle congestion and preventing injuries. By automating tasks that no longer require human involvement, AGVs contribute to a safer working environment.
Conclusion: Automated Guided Vehicles (AGVs) offer significant advantages in warehousing and manufacturing operations. From increasing efficiency and productivity to providing consistent costs, flexibility, space optimization, and improved safety, AGVs have transformed the way tasks are automated. By adopting AGV technology, businesses can enhance their operational capabilities, improve worker satisfaction, and ensure a safe and productive work environment.